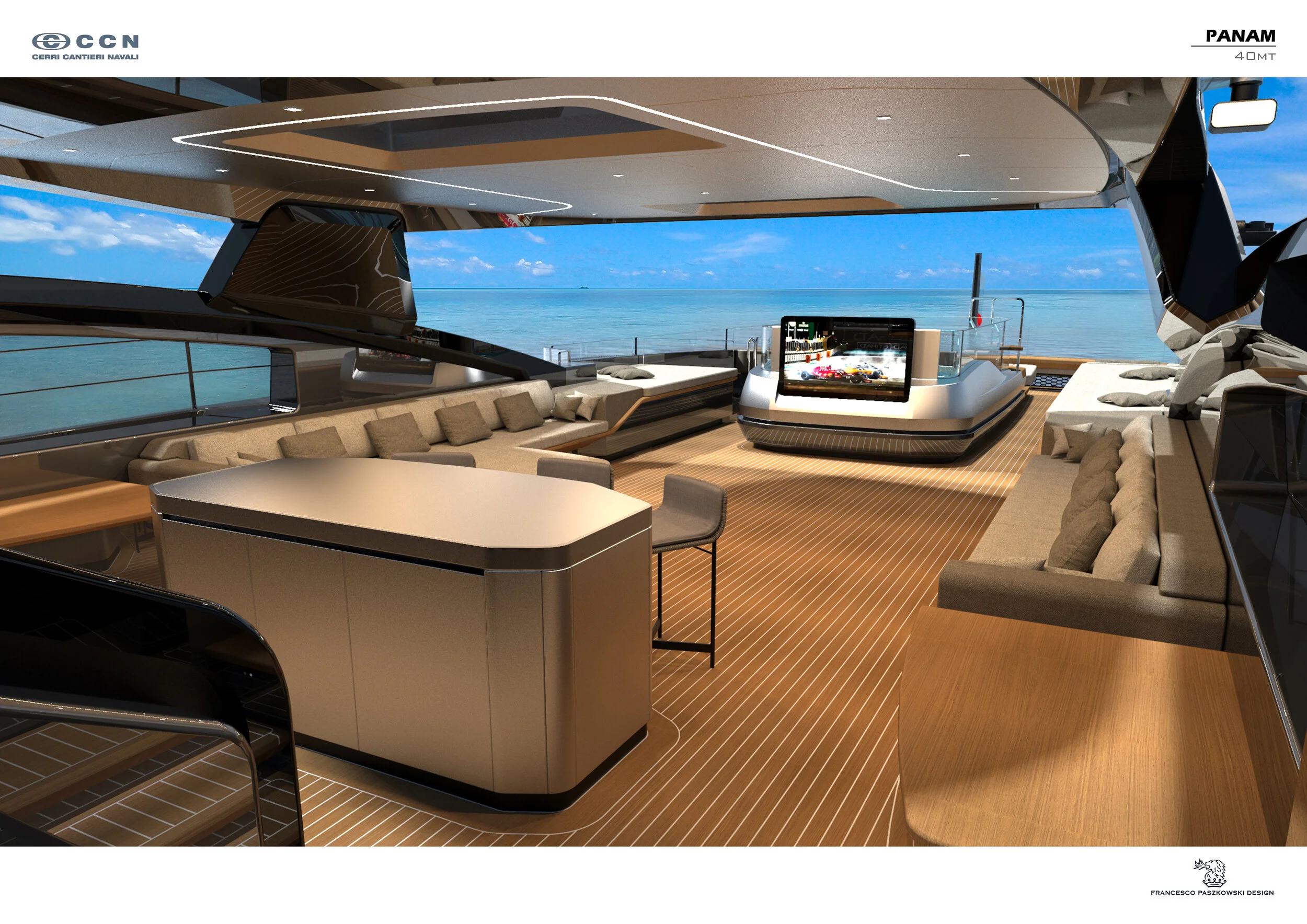
CCN Panam c4002
Progress Report - 01 mar. 2021
1. GENERAL SITUATION
The vessel has been re-launched since the last update. Moored stern to the dock at the Baglietto facility in La Spezia.
Although works have been steady, we are in the final stages of completion of all areas onboard. Internally, finishing works continue in all areas. There are no single areas to highlight that are actually ready for any form of acceptance inspections. Internally the yard has begun the process of minor defect rectification identification, although none of these works seem to have been undertaken to date.
2. EXTERIOR
Rather disappointingly, much owing to adverse weather conditions, the progress with advancement towards completion of the external areas is slow.
From receipt of the previously issued paint report carried out several weeks ago, very little on that report has been addressed, almost nothing. We believe that over these next 6 weeks, where we will be undertaking a huge effort of thoroughly test and operate all onboard equipment, this defect list is likely to grow significantly. This is totally normal as we start, run, test and push the various equipment and system components.
A series of dock trials are already outlined and the system-system process of sign off will begin. A point-by-point list will be kept and updated as we advance through the process. This will be shared between all parties.
Ultimately, this list will form the final defects at a stage of delivery to be yet confirmed. These will then go on, if un-rectified at the time of delivery to form the outstanding works list - more often referred to as the list of minor non-conformities. We hope to not have any major non-conformities.
3. INTERIOR
The thrust of the works seems to have been aimed at the beach club area, tender garage and engine room. The entrance and stairwell leading down form the main saloon to the aft. lower deck areas have taken form although a good amount of works remain to be done.
The tender garage, save some deck fittings appears almost complete.
The beach club area is missing overhead panels and also the track decking. Also remaining are outfitting works in the two aft quarter technical spaces housing the hydraulics and shore power converter.
The green garden in the main saloon is currently in the process of being installed and it’s completion anticipated, likely ahead of your receipt of this report. Once done, the final installations of the dining room and main saloon areas can take place.
The outfitting of the wheelhouse is another area that just seems to drag on. At the time of this report (and sea trials) various panels, overheads and leather features are not onboard. Rather than outline everything in this text section, we have attached under the text section a list of items noted during the sea trial. The yard will receive this list separately from this report, so they action the points.
4. SEA TRIAL REPORT (PRELIMINARY) LROS SURVEYOR AND CREW ATTENDANCE ONLY
Location: Baglietto Yard, La Spezia, Italy
Timings: 0900 hours, duration roughly 8 hours
Conditions: Fair, Variable winds 2-3 with clear sky sea state 2 decreasing.
Persons: Yard Personal and Contractors 25 in total
Particulars:
The vessel’s main tender and bow rescue tender and PWC’s were not embarked. The vessel departed the mooring and proceed to sea. Motoring trials were conducted with the presence of an MTU engine technician.
A series of rpm steps were conducted, from idle to full ahead course with reciprocals runs were conducted. The full data will be relayed to us from the onboard engineers once collected.
A four-hour endurance test was carried out. This is part of the LRoS (Lloyd’s Register of Shipping). This is a test where the main engines are run at full load for a period of four hours and all temperatures and alarms are noted.
The vessel’s anchoring system was not able to be tested at this time. This was one of the primary tests required by the classification society, so another trial will have to take place to allow them to inspect the deployment and retrieval of the anchors and associated equipment.
Also observed running were the main power generators. For some reason the yard chose to maintain both generators running. It was only when the chief engineer pointed out the high engine coolant on the port side generator, they shut down and run on the single starboard side generator.
The water maker was not test operated at this time.
Most of the navigation equipment was tested, electronic charting, navigation aids, radios, transducers etc. were mostly seen operating although much of the equipment still requires proper calibration.
Low and high-speed manoeuvring tests were carried out. S-turns and 360-degree circles were driven to see how the yacht behaved at these different speeds, both with and without the stabilisers functioning. The yacht appears to ride well during these tests, feels solid. With the yacht’s inherent list towards the aft starboard quarter, a more precise series of assessments needs to be undertaken drug the next set of sea trials. As well as essentially a zeroing or resetting of the onboard parameters in relation to trim and list, coupled with the resetting of the associated datum points for measuring, a much more detailed series of results will be delivered. Until then, the readings and data should be considered a benchmark point and for referencing purposes only.
The hinges were run up full speed almost immediately after clearing the VTS channels in La Spezia. The following readings were taken at the midpoint during the endurance test (2 hours) into the running at full speed. No high temperatures were noted on any of the propulsion lines, bearing temps etc. The engine room maintained a good working temperature with no isolated hot spots noted. The engine room ventilation is controlled manually by the chief engineer from the engine room itself. No remote station control was seen. Nothing in the way of temperature of pressure regulation noted.
As you will see from the pictures below, some components will need to be further investigated and rectifying actions taken to comply with the various LRoS regulations in this respect. Please see Thermographic FLIR images, taken with a FILR TG165 handheld camera (E0.95).
The following values were recorded at the commencement of the sea trial. These obviously altered during the trial run, notably with the fuel decreasing significantly with the 4 hours full speed endurance run.
What should be noted is that the yacht was noticeably trimmed aft and to the starboard quarter. This was despite being roughly 2000 litres more consumables on the port side and having no tender embarked.
The yards engineering team was also moving fluid contents onboard during the trials by means of the fuel purifier so it is difficult to make assessments or comments on this. Also, no stability booklet information has been provided, no tank soundings were done, so the figures are totally reliant on the AMS sounding calibrations. We have no way of knowing at this stage the accuracy of the programmable sound curves generated by a tank with a single sensor input. Variations in trim and heel are highly likely to be providing us with incorrect data. Something that will not happen on the delivery/owner sea trials.
It’s relatively clear to us that the yacht is much in need of further sea trials and systems integration/calibration in order to illuminate many of the system interfacing issues that seem to remain.
The following data was recorded during the trials. At the commencement of the four-hour endurance trials, the yacht at max speed/rpm was observed to reach a maximum speed of 27.2 knots (SOG), with no active fins or active interceptors.
After four hours of boring fuel (approx. 1500 l/ph.) so less 6000 litres, the yacht was seen to achieve 28.4 knots (SOG). With no active stabilisers or interceptors.
Although not verified by me, the yard report with the stabilisers off, and interceptor active, they achieved 31 knots.
The main trust in our opinion that needs to be addressed is that of the load line assignment - vessel trim and list. What seems to be fast apparent is that the central tank designated fuel oil (tanks 6) referred to in the contract as “extra range” tank, and is significant in capacity, needs to be filled, i.e.: the yacht needs to be fully fuelled and brough to the conditions designated by the load line conversion and the stability booklet, to fully ensure that the vessel is in full compliance with the build contract. When at “departure conditions” we need to ensure that the yacht remains within her design parameters, otherwise the likely consequence of this not being achieved is to make necessary reductions in the amount of consumables onboard i.e.: take fuel off the vessel. This will of course result in a reduction in the range or endurance performance figures.
As indicated to us by the yard, the vessel at the time of trials was recorded at around 255t - the build specification states trials to be done in no more than 235t.
In plain context, that means the yacht is heavier than it should be. A more in-depth look into the cause off this is needed, although we can say with a high degree of certainty at this stage, there is no doubt that the yard will try to put the responsibility for this onto the client and or interior designers. What is transmitted or communicated to the yard in this respect should be carefully managed by us internally. Depending on the outcome of this topic, the yard may even have to increase the weight of the vessel in order to achieve the even trim/list needed at departure conditions by means of adding fixed ballast. Again, this could have consequences for speed and range in real terms.
This list/trim subject could prove to be of particular importance. Although we would stress we at a very early stage of discussion on this subject and have limited information from which to work; the naval architect and yard personnel have all advised that the vessel is designed to be used at speeds in excess of 19 knots, without the stabilisers in use. In fact, either centred of actually switched off. If this is the case, and this is the design criteria, then the question of correctly trimming the yacht is of paramount importance, otherwise she will be underway at cruise speed (25 knots) potentially with a list only able to be compensated by the movement of fluid. At high levels of capacity, this may not be possible. More will follow on this subject.
5. FINDINGS AND RECOMMENDATIONS
CERTIFICATION and GENERAL COMMENTS
No stability booklet has yet been supplied to the surveyor for assessment. This should be provided as soon as possible to establish the loading criteria and various other interconnected variables.
Vibration and a degree of flexing noted on the upper deck aft quarters. Carry out vibrational testing in these areas.
Swimming pool appears to not yet be operational. Complete the installation and testing.
Upper deck central bar not installed.
Beach club decking, overheads and shell doors not yet installed.
Wheelhouse not yet fully installed or operational.
There are lot of missing pipe identifying label sand directional flow arrows. Many valves and through hull fittings are missing identifying marks/labels. The yard is to complete this as soon as possible as per technical specification requires.
TANKS
Questions surrounding the class/flag stance on use of the swimming pool. Sea water is pumped into the pool, which reportedly uses a chlorine dosing system. The water is then to be directly discharged overboard after use. Confirm how D1 compliance is achieved even through this is not considered at BWT system - the reality of supplying sea water, treating it, then discharging it must confirm to MARPOL requirements. Shipyard to supply information on the compliance of these regulations and the operational parameters as a consequence of these.
The launching and recovery of the tender has not been seen yet. There is a compensation tank fitted on the port side of the vessel. This is reported as being around 5000 litres in capacity. It seems rather large considering the weight of the tender. A dedicated pump for filling and discharge so fitted and seen in operation during the sea trial. Care should be taken in this respect. This is not a sea water ballast system and should not be used as such to alter the natural trim/list of the vessel at any point. This would be in direct T1 directions of Annex IV MARPOL regulations.
FUEL SYSTEM
Tender feeling gun motor pump control - loose and unsecured cable leading upwards to the overhead. Properly secure.
No proper holder or mount noted for the tender feeling gun. Provide permanent support in upright position for the feeling gun.
STEERING
No manual or emergency helm override noted to the autopilot. As per flag regulations install and test prove operations.
BILGES
Various leaks found in the engine room (centre bilge) - it appears to be fuel. A temporary transparent hose is currently fitted, it’s purpose is not entirely clear. We will monitor the problem.
PLUMBING and PIPING
Compressed air blowdown for main sea chests has bayonet connections, check the provided hoses can fit to serve this arrangement and that these fittings can be properly isolated in the event of failure.
Top mounted box located port side engine room forward (Selmar unit) secured with velcro straps. Properly secure this unit.
VENTILATION
Both port and starboard side generators have protruding battery boxes aft, at the underside of the generators. The overhead ventilators are supplying a good portion of their air flow directly down onto these boxes. Recommend the closure of the aft and side sections of these battery boxes to prevent the cables and terminal from accelerated corrosion.
MAIN ENGINES
Yellow - Main engine starboard side gear oil filter clogged and yellow advisory MTU alarm present. Rectify and prove operations.
ENGINE EXHAUSTS
Main engine exhaust temperatures were seen to be nigher around the upper welded section close to the water injection spray ring. Please see thermal images. This is something that should be closely monitored. Possible rectifying actions may be needed.
Port side lower hull box sections of the main engine exhausts were observed to reach upwards of 70 Degrees Celsius. Given the cool sea water temperatures of present, it is highly likely that these temperatures will only rise in warmer times. Provide protection inboard of these structural boxes and monitor for rising temperatures during operations. Regulation of the sea water injection circuit may be needed or indeed more cooling water injected to the system.